Laser Structuring
DLIP enables laser structuring on almost any material with highest precision and record speeds.
Laser Structuring
In general, laser structuring involves scanning the surface to be processed in a defined manner with the aid of a laser beam (focused or defocused) and thus locally heating, melting or ablating (material removal) the material at the point where the energy is injected by the laser beam.
In this way, depending on the laser-material interaction, a certain surface structure or micro-profile is created. But that is not all – due to the energy coupling into the surface, a direct influence on material properties (e.g. microstructure, oxidation behavior and phase formation) can be achieved in addition to the pure topographical surface design by means of laser structuring. This way, besides the pure topographic manipulation, a further degree of freedom regarding the functional design of surfaces is available.
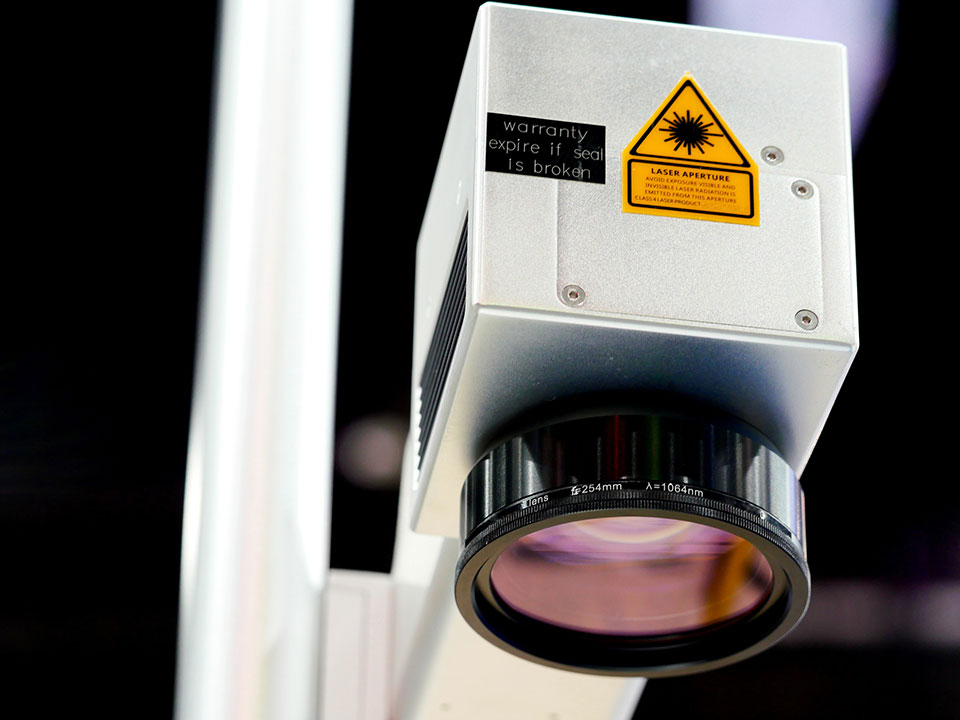
The efficiency of the energy coupling during laser structuring depends mainly on the absorption behavior of the material surface and can be influenced by the choice of the wavelength (from ultraviolet to infrared) of the laser system used. Thus almost any material can be processed by laser radiation.
Besides wavelength and other important parameters, laser systems for laser structuring differ, e.g. with respect to the active laser medium and type of excitation (e.g. gas laser, solid-state laser and diode laser), the laser power (from a few W to several kW) or even the mode of operation (continuous or pulsed). Especially laser structuring by means of pulsed laser systems is gaining more and more importance nowadays, also in industrial production. This due to the fact that pulsed laser operation in short (nanoseconds) to ultra-short (pico- to femtoseconds) times/pulses makes enormous laser power/pulse energies available, which allows for completely new possibilities regarding material processing.
Advantages of laser structuring
As an optical, high-precision and contact-free technology for surface processing, laser material processing or laser structuring is definitely one of the key technologies of the 21st century, offering a wide range of solutions and enormous advantages in numerous fields of application.
The laser structuring process allows the properties of machine and tool surfaces to be specifically improved in a wide range of application fields. This is achieved with a broad spectrum of machinable materials, clean and environmentally friendly process control, a process-related good spatial resolution and high process speed. The advantages of laser structuring compared to other technologies at a glance:
Contactless
Nearly “wear-free” technology (no mechanical tools required)
Sustainable & easy integration
Since it can be integrated into existing production lines. No changes to the existing process chain and products for processing by laser are necessary.
No chemicals & environmentally friendly
Only the already existing material surface is used. Additional coatings with possible chemical waste products are not necessary.
Fast / process speed (m²/min)
Laser structuring reaches record processing speed compared to other processes.
Automatable
Laser structuring can be 100% automated and is therefore ideally suited for production lines in mass production.
Precise
Depending on the laser structuring technique, structures of a few millimeters up to a precision in the nanometer range can be produced.
Laser structuring process
The most common method of laser structuring is certainly the so-called laser writing. Here the laser beam is directly focused by a lens and guided over the surface to be processed.
Depending on the degree of focusing and the selected “writing grid”, a certain surface structure or micro-profile (e.g. lines, dots, etc.) is created.
The process speed of this method of laser structuring is so far limited by three parameters using pulsed lasers:
- Structure size to be generated: The smaller, the slower. Minimum structure size is limited by wavelength, beam quality and lens error.
- Laser parameters: Interaction of spot size, pulse energy and frequency
Speed and precision of beam guidance: Today, galvano- or polygon scanners are used for this purpose in order to minimize process times as far as possible.

This fact poses technical process challenges to classical laser structuring in terms of economic feasibility for small structure sizes < 20 µm (a human hair has a diameter of approx. 60 µm).
In this context, a novel laser structuring technology, called “Direct Laser Interference Patterning (DLIP)”, is to be mentioned, which has attracted increasing attention in recent years through several renowned technological awards and numerous publications.
The reason for this is the enormous width of the covered size scale of the achievable surface structures, which reaches from the sub-µm to the upper µm scale, the laser-related possibility to process almost any material and to reach process speeds of up to m²/min.
Now have a look at how it works: Direct Laser Interference Patterning (DLIP).
Applications Laser Structuring
Laser structuring can be applied to almost any material to create almost any geometric structure.
Depending on the wavelength, power and pulse length of the used laser system, the following materials can be processed:
- Metals (e.g. hard metals, steel, copper, aluminum, tin, silver, etc.)
- Plastics (e.g. thermoplastics such as PC, PET, PMMA; thermosets such as epoxies, polyesters, polyurethanes and also elastomers)
- Ceramics (e.g. silicon nitride, aluminium oxide etc.)
- Glass (e.g. borosilicate glass, quartz glass etc.)
Get to know concrete application examples now, such as lasers structuring of electrical contacts, laser structuring in the field of medicine, or contact us directly about your application!
Do you have any questions?
Contact us now. Our experts will be happy to help you!
Big changes start on a small scale.
Contact the SurFunction GmbH team of experts now. We will be glad to show you how you can start into the next generation of your products with DLIP!